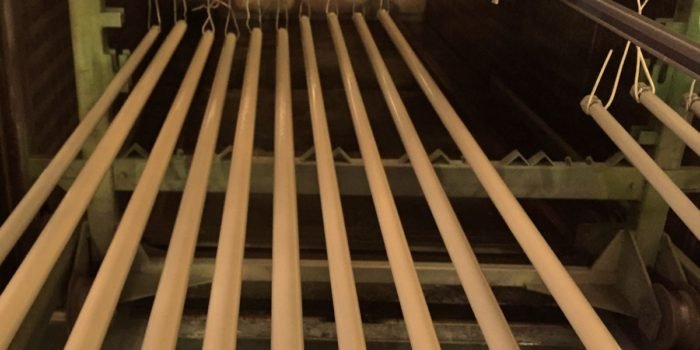
Purisan™ PVDF Chemical Mixers: thick coated shaft with injection molded blades
For many applications PVDF coatings provide a high purity surface while eliminating corrosion problems. However, a completely coated mixer is not the optimal material choice. Consider the leading edge of impeller blades. During daily use this surface comes in contact with the solution and all that it contains. Powder coating along the leading edge of the impeller are prone to rapid wear and exposure of the metal substrate leading to process contamination and mixer failure.
A common work-around is to increase the thickness of the coating on the blades, but with a specific gravity of 1.8 or more for a fluoropolymer coating this can lead to serious imbalance issues.
At Nile Polymers we have a better approach. We replace the coated metal impeller with a fully injection molded impeller. The injection molded blades contain no metal and the impeller attaches to the shaft with a simple threaded connection. The threaded connection allows for a quick change-out of the impeller if the manufacturing process changes and a different size impeller is required or if someone left a wrench in the tank and the impeller becomes damaged. It happens. If your mixing application could benefit from Kynar® PVDF on all wetted surfaces then consider our Purisan™ PVDF mixer. Combining a Kynar® PVDF powder coated shaft with an injection molded Kynar® impeller, our Purisan™ PVDF chemical mixers provide the purity, corrosion resistance, abrasion resistance and service life you require at a price you can afford.